Major Projects
Albany International (October 2023 to December 2023)
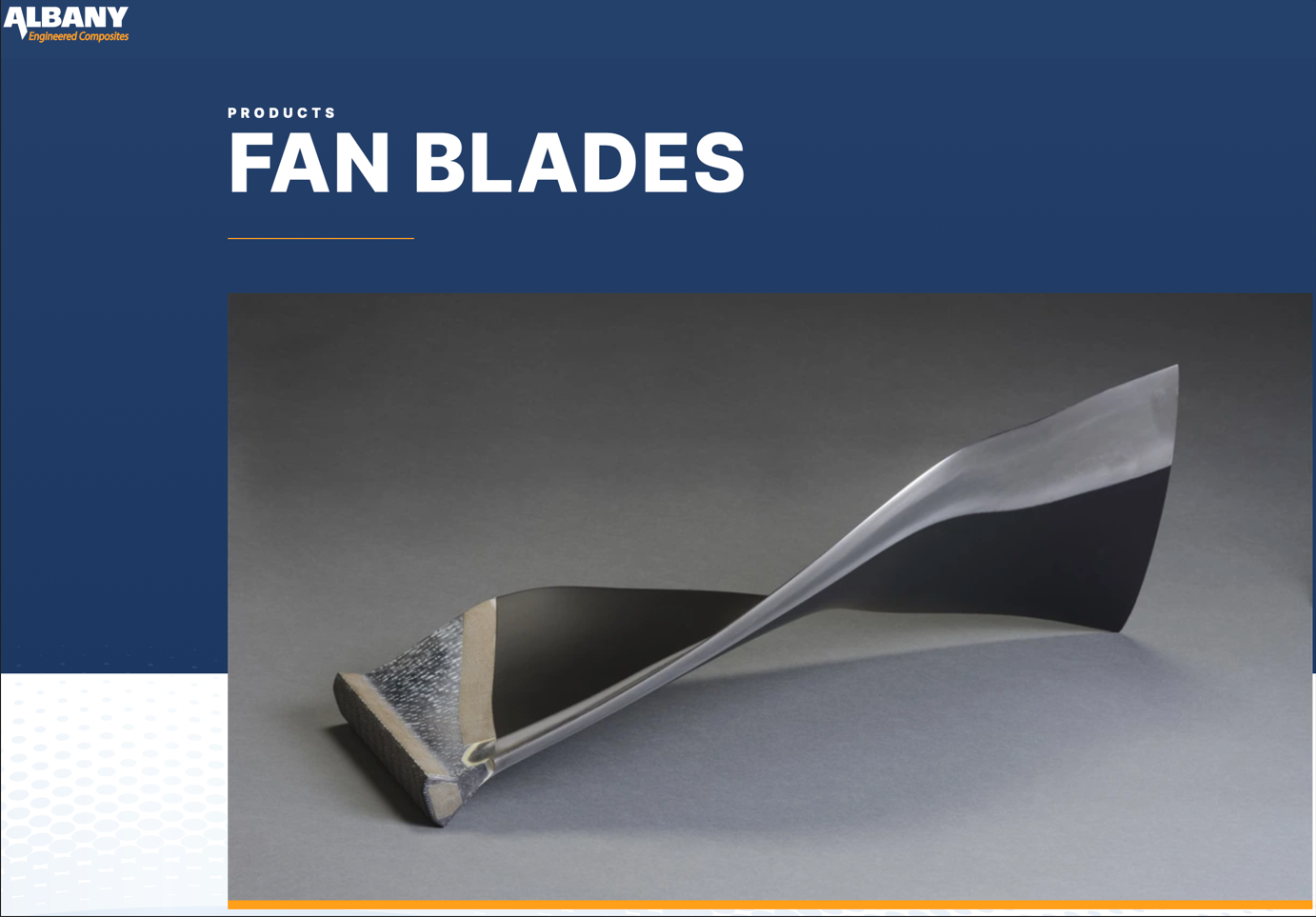
In the period spanning October to December 2023, my colleague and me conducted a meticulous Life Cycle Assessment (LCA) on fan blades for Albany International, specifically comparing the environmental footprint of 3D woven carbon composite fan blades with titanium alternatives. The assessment involved an extensive literature review to comprehend the intricate manufacturing processes of 3D woven carbon composites, ensuring a comprehensive understanding of the materials under scrutiny. Gathering comprehensive data on both carbon composite and titanium fan blades, I executed a parallel LCA study using OpenLCA software. The “Cradle to Gate” analysis evaluated environmental impact across five crucial TRACI categories, including human health, resource depletion, and ecosystem quality. This thorough analysis enabled the quantification of the environmental performance of both materials, delivering valuable insights that can inform future material selection strategies for Albany International.
The study successfully unveiled key aspects of the environmental impact associated with 3D woven carbon composite and titanium fan blades, shedding light on their respective advantages and challenges. By utilizing OpenLCA software and focusing on the “Cradle to Gate” perspective, the assessment provided a holistic understanding of the life cycle environmental implications of these materials. The findings not only contribute to the ongoing discourse on sustainable manufacturing but also offer Albany International actionable insights to enhance their decision-making processes regarding fan blade materials, with the potential for positive implications on both environmental conservation and manufacturing efficiency.
Topic: Real life 3D Working Model of a Sliding Gate Assembly
The project on the dynamics of a sliding gate assembly showcased a comprehensive application of mechanical engineering principles, focusing on the design and functionality of a motorized gate system. Utilizing SolidWorks for 3D design and animation, the project began with the conceptualization and detailed modelling of the sliding gate, considering factors such as size, weight, and structural integrity. The integration of a motor for remote operation was a pivotal aspect, with careful consideration given to motor selection and compatibility with the overall system dynamics. A noteworthy highlight was the project team’s hands-on experience at a gearbox manufacturing facility, which informed the design of a custom gearbox tailored to the sliding gate assembly’s specific requirements. The meticulous 3D modelling and virtual prototyping in SolidWorks ensured the seamless integration of the gearbox, contributing to the overall efficiency and reliability of the motorized sliding gate system.
In conclusion, the project not only successfully employed SolidWorks, 3D design, and animation techniques to create a sophisticated motorized gate with remote control capabilities but also demonstrated a practical application of theoretical knowledge. The incorporation of insights from the gearbox manufacturing visit added a layer of precision to the project, emphasizing the importance of real-world experiences in enhancing engineering solutions. This comprehensive exploration of machine dynamics not only resulted in a functional and efficient sliding gate assembly but also provided valuable hands-on experience in tackling practical engineering challenges.
Topic: Proposing an automated Boat Rovering System
In the realm of Machine Design 2, a ground-breaking solution to the physically demanding sport of rowing was devised – the Integrated and Automated Boat Rovering System. The conventional act of rowing, despite its exhilaration, presented a significant challenge due to its demand for substantial physical strength and endurance, limiting its accessibility. The Boat Rovering Mechanism, focusing on scull rowing with two oars per rower, was introduced as a response to this limitation. The system ingeniously employed a worm gearbox mechanism, with a shaft connected to a worm gear initiating a chain reaction of mechanical movements. As the shaft set into motion, the worm gear rotated, transmitting force to a worm wheel connected to a handle, and subsequently, to the oar.
This orchestrated movement propelled the boat forward or in reverse, providing a revolutionary and automated alternative to traditional rowing, effectively addressing the physical limitations associated with manual rowing and enhancing the accessibility and enjoyment of the sport. In essence, the innovation in Machine Design 2 represented a paradigm shift in rowing, where engineering principles were leveraged to make this exhilarating activity more inclusive and user-friendly. The Boat Rovering Mechanism, showcasing the transformative power of machine design, exemplified the integration of technology with sports and demonstrated how thoughtful engineering can enhance and diversify recreational activities.
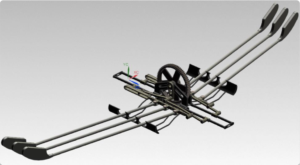